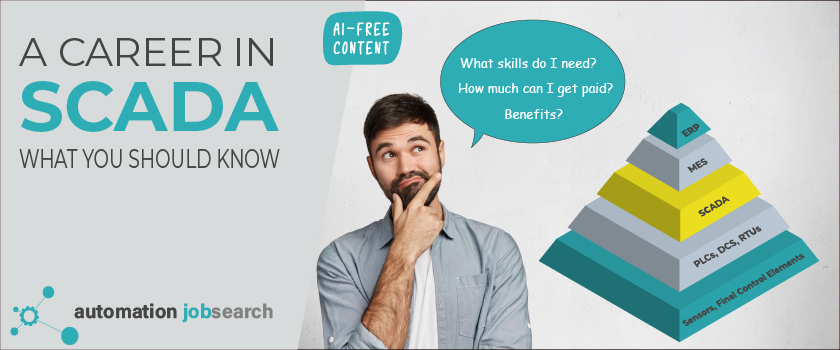
Thinking About a Career in SCADA? Here’s What You Should Know
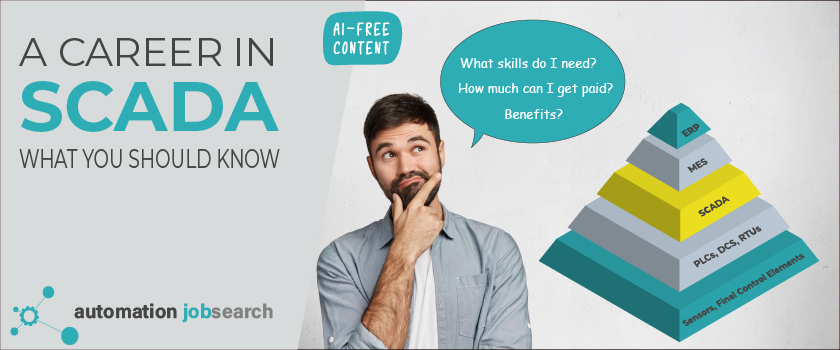
Are you thinking about moving to a career in SCADA? Are you graduating soon or considering a career change?
Despite its enormous contribution to modern industry, SCADA is a field of engineering that is is not well understood. It has a reputation for being technically demanding, requiring a broad and deep IT-based skill set that can seem overwhelming to many. The long learning curve associated with mastering these skills can be off-putting to newcomers.
SCADA engineering, unlike many professions, requires a diverse range of skill sets, including IT, control theory, industrial control systems, and data science. It draws on skills that are acquired by academic level study while also requiring technical skills more commonly associated with trade schools such as PLC configuration.
Obviously, this has created a cloud of confusion around the SCADA profession. Many people are unsure of how to enter the field, what steps to take and what skills they need. This confusion makes it difficult for aspiring SCADA engineers to find a clear path into the profession.
In this article, we will try to answer all the questions you might have about SCADA engineering, including;
- What is SCADA (and what it is not)
- What type of companies do SCADA engineers work for, and what exactly do they do
- Which types of industries employ SCADA engineers
- What kind of technical and mental skills do I need to work with SCADA systems?
- Do SCADA engineers get paid well?
- What are the main benefits and drawbacks of working within the field of SCADA?
- What kind of qualifications and training do I need to get a job in SCADA
What Exactly is SCADA?
You probably know that SCADA is related to industrial automation but where does it actually fit into the big picture?
The term SCADA can mean different things depending on the context. In some cases, it refers to a specific SCADA product such as Ignition or InTouch. This is a server hosted software that comes with a suite of SCADA functions including HMI (Human-Machine Interface), historians, databases and is used to pull data from various control systems and devices using different methods and protocols.
However, the term SCADA is sometimes used as a broad term to to refer to the entire control system architecture, including the field instruments instruments and the network infrastructure.
For example, a well-known book defines SCADA as
A collection of computers, sensors, and other equipment interfaced by telemetry, to monitor and control processes.
INST ENG handbook Process Control and Optimization 2006 4th Edition.
Probably the easiest way to conceptualize SCADA is as a high level control system that operators at a layers above the control level (ISA 95 Model). In many cases, a SCADA is used to monitor multiple facilities that are separated geographically by great distance. The devices that interface with SCADA are PLCs, RTU and virtually any data producing industrial equipment or system from which information is needs to be exchanged, this may even include local DCS systems.
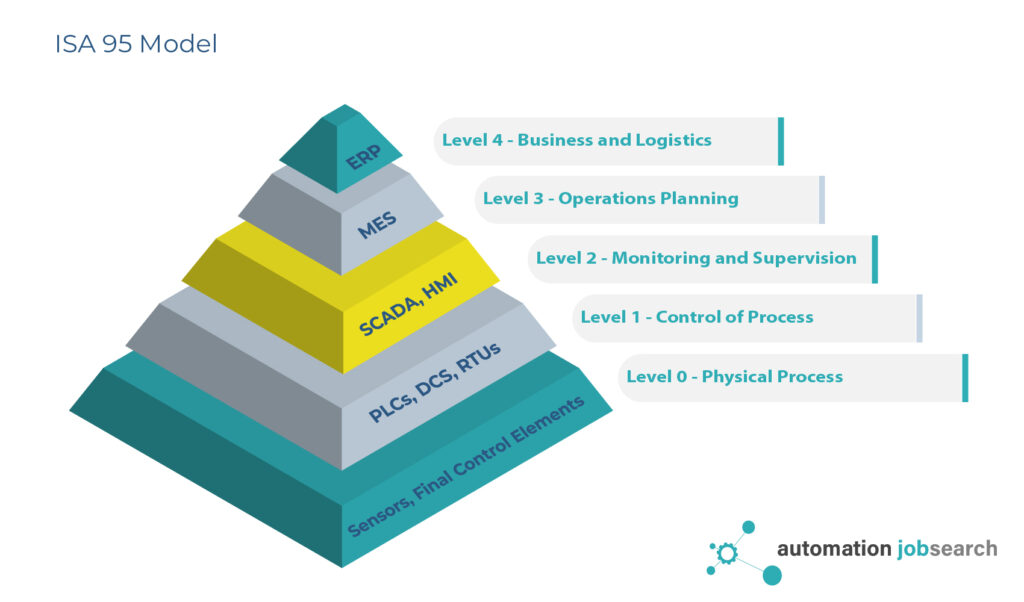
Modern SCADA products are increasingly marketed as “enterprise solutions” that operate at a level above traditional DCS/PLC systems. These solutions monitor multiple facilities across large geographical regions and are also used by company personnel outside of the plant’s operations team.
SCADA systems are becoming more integrated with company IT, with recent products incorporating MES, QMS, and other systems traditionally considered part of the ERP level. This integration is often described as a merging of the top three layers in the ISA 95 model into a single, unified layer.
The basic components that make up a SCADA infrastructure include:
- SCADA System software (server hosted)
- HMI Station / Clients
- PLC, PACs, IPC and DCS
- Networks / Telemetry
- Instrumentation/Drives/Robotic
SCADA System software – Server-hosted software, normally includes database and Historian, Alarm management and toolsets to allow engineers to configure data interface for many different automation systems. Some examples of SCADA products are;
- Emerson Open Enterprise Suite
- GE – CIMPLICITY
- GE – iFix
- Intouch (AVEVA)
- WinCC (Siemens)
HMI Station / Clients – Human Machine Interface for SCADA users such operators, supervisors. HMI can be web based (such as Ignition SCADA) or dedicated clients stations on a local network.
PLC, PACs, IPC and DCS – Industrial automation systems that execute the control functions on the shop floor level taking inputs from transmitters and controlling the process by manipulating valves, drives and other final element.
Networks / Telemetry – This includes the entire network architecture that supports communication between all devices within the SCADA architecture. Including switches, firewalls, routers, cables and any other network components.
Instrumentation/Drives/Robotic – Transmitters and final elements that interact directly with the process.
Is SCADA the Same as DCS?
Not really. While the hardware components and network architecture of a SCADA system may appear the same as DCS there are important nuances that distinguish SCADA as a very different concept. A full comparison between the systems would require a dedicated article ,however, the most significant differences are;
- Performance and real time communications
- Supervisory vs control Functions
- Spatial arrangement and architecture size
- Licencing models
- Industry leaning and preference
- Deliver model – CSI vs MAC
Real-Time Communications
SCADA systems tend to use event oriented protocols and are more tolerant of low bandwidth/high latency connections. DCS systems tend to use simpler real time protocols such as UDP and are less tolerant of low bandwidth/high latency communications..
At the plant control layer of industrial control systems, where speed and efficiency are critical, UDP is often chosen for its simplicity and reduced processing overhead, most DCS use some form of UDP for controller communication. In addition, DCS tends to be more optimized for integrity and performance, automating process facilities that required medium to fast response times with high availability.
Less Control Function and More Supervisory
Early legacy SCADA deployments were primarily used for plant floor automation. However, the role of SCADA has moved to a more supervisory level. SCADA is generally used less for control purposes and more for high-level monitoring and interfacing with ERP and MES systems.
In modern applications of SCADA, it is only used for control functions that cannot be automated such as scheduling production batch’s or opening and closing valves on remote pipelines i.e. manual operator actions taken in response to emerging scenario such as changes in commercial obligation, environmental, safety and political events that impact that require the end-user to take action.
Spatial Arrangement and Architecture
A DCS tends to be deployed on a single facility or campus, while a SCADA system tends to cover anything from a facility to an entire state. SCADA is often deployed for systems that cover large geographical areas such as railway, pipelines and other large infrastructure projects.
Licencing
DCS is licensed on a tag basis, whereas SCADA is typically licensed based on the number of HMI clients or server installations, often offering unlimited tags. This makes DCS impractical for supervisory roles despite its technical capability, as its performance and licensing model can be highly costly and impractical.
It is not uncommon for some SCADA to handle millions of tags (e.g. rail monitoring systems), while a single DCS system rarely exceeds 10,000 tags.
Industry Leaning and Preference
DCS tend to be widely used in continues and batch type processes, such as chemical, pharmaceutical, oil and gas. Here the real time performance of UDP communication is leveraged, along with high integrity control to controller communication.
In addition, DCS from leading suppliers often includes a suite of advanced functions that are tailored to process industries such as advanced process control (APC), PID loop tuning applications, Alarm Managment and Asset Managment.
Delivery Model
DCS is almost always delivered within the framework of a MAC (Main Automation Contractor) delivery model, where the automation supplier is responsible to manufacture, build, and commission the entire automation system.
While some DCS products are available through distributors, most are not and can only be installed by the actual automation supplier through comprehensive engineering and service contracts.
This is known as a “Single Supplier Solution” and is popular in industries where the process design is well established and facility designs can be easily replicated and duplicated (e.g. offshore production, chemical plants).
SCADA, on the other hand, is typically developed by a SCADA developer/supplier, but the design and integration of the system are carried out by a control system integrator (CSI).
Most control system integrators are not tied to a specific SCADA package, offering flexibility to the end-user. This approach is generally better for end-users who need to automate more complex and unique processes, requiring a more agile development approach (manufacturing, automotive).
What are the Different Engineering Roles in SCADA?
The field of SCADA can encompassed many different role, and companies will offer positions of varying specificity based on their size and operating model. Some engineers specialize heavily, focusing solely on specific aspects of SCADA like databases, historians, or industrial networks.
Other engineers may have broader expertise, enabling them to make informed decisions independently while occasionally seeking support.
The extent of which a role is specialized typically correlates with company size, smaller automation firms often expect engineers to possess strong general automation skills beyond SCADA alone.
While we have listed several commonly encountered job titles, it’s important to note that this serves as a guide, and many engineers may have responsibilities that span or overlap across these roles.
SCADA Developer
As with all automation technologies, there are individuals responsible for creating and developing the SCADA at the product level. They focus on backend software development to create the tools and interfaces that SCADA engineers use to integrate client systems.
These roles are typically the furthest removed from the operational processes and generally have limited involvement in SCADA integration, except when resolving significant issues that require support. Responsibilities in this role often include low-level coding, building drivers and firmware, and developing patches and updates. An example of some SCADA development activities include;
- Driver and Firmware Development: Developing software components and modules that expand or improve expand on the SCADA package functionality.
- Patch Creation and Deployment: Developing updates and “hot fixes” to address software vulnerabilities, enhance functionality, and fix bugs.
- Product Support for SCADA Engineers: Providing remote technical assistance to SCADA engineers on site.
SCADA Engineer
SCADA engineering is a specialized subset of control system engineering that focuses on SCADA system integrations, database connections, historian configuration, and interfaces for different data streams from the process.
A SCADA engineer primarily deals with SCADA software configuration, interfaces, and networking. They tend to work less on other automation systems such as PLCs and instrumentation, PLC, or IEC61131 based programming. Typical tasks and responsibilities of SCADA Engineer include:
- Analysing process design inputs (e.g. P&IDs and UFDs) and developing HMI graphics.
- Designing interface solutions for external control systems and automation devices to be interfaced with the SCADA.
- Troubleshooting TCP/IP, Modbus, OPC, and network communications issues.
- Configuring OPC servers to collect data from various sources located at the plant control level.
- Configure, troubleshoot, and commission L2/L3 network devices, such as servers, workstations, switches, firewalls, and routers.
- Supporting I&C teams to troubleshoot field device issues and commissioning of new instrumentation (e.g. applying logic forces and bypasses in the live logic, or simulating process inputs).
- Reviewing and analysing alarms and events to investigate plant performance issues or process trips
- Managing firmware updates and patch updates for SCADA software and associated hardware and network infrastructure devices.
Depending on the role, SCADA engineers can work in an office-based engineering role or site-based in a commissioning/service role, or sometimes a combination of both. Large automation companies usually have separate service and engineering teams, although it is not uncommon for individuals to work in both domains.
SCADA Designer / Architect
SCADA roles can sometimes focus purely on detailed design, which involves designing the SCADA network infrastructure, specifying the type and location of all network components. This type of role is often referred to as a SCADA Designer or SCADA Architect.
Typically, these roles focus more on detailed design work rather than onsite activities and may also overlap with sales positions, such as a Solutions Architect, contributing to early concept designs and tender processes before contract awards.
SCADA Engineers in this type of role are generally very experienced and have excellent network skills enabling them to design complex, multi-topological industrial networks, subnets and VLANs. This design process involves many design inputs including the plant location of ICS equipment, environmental constraints, and end-user requirements for network manageability, availability, and latency.
Control System Engineer / Automation Engineer
Many engineers who work with SCADA systems may not exclusively focus on SCADA. Instead, SCADA is just one aspect of the various systems they work with. As a result, they may not officially hold the job title of “SCADA engineer,” but this doesn’t mean they lack competency in this area.
Control system engineers should possess a wide range of skills related to automation systems, including instruments, PLCs, and networks. They should also have a strong proficiency in DCS or SCADA and be able to apply their skills as needed.
Control System Engineers tend to be much closer to the process; that the other roles described above. They work closely with operations teams and process disciplines, developing a good understanding of the process, which enables them to specify, develop and fine tune control solutions.
What Skills and Mental Attributes are Required for SCADA Engineering?
If you gathered 100 SCADA engineers in a room and listed all their skill sets, you would likely cover almost every programming language and IT skill known. However, this doesn’t mean you need all these skills to work in the profession.
We’ll discuss the necessary skills in terms of both hard and soft skills, as both are crucial.
We will cover two major categories of skill sets needed for a career in SCADA:
IT, Programming, and Scripting Skills for SCADA: This includes all the “hard skills” typically encountered by SCADA engineers and developers. You don’t need to be an expert in all these areas. Many developers have a moderate level of competency in some skills, while others have a focused specialty and expertise in a few areas.
Note: As we are focusing on SCADA engineers, we’ve tended to exclude or give less emphasis to skill sets related to field devices and technology at the field level, such as instrumentation, motors, and robotics. However, depending on your level of specialization, you may need some knowledge in these areas.
Traits and Mental Skills: We have highlighted key mental traits and behaviours important to the field of SCADA (or general automation).
Programming Skills Needed for SCADA Engineering
- C/C++ is used for backend SCADA development and embedded systems.
Also increasingly used for industrial computers (IPCs) and some PLCs such as Beckoff support C programming (TC1300 | TwinCAT 3 C++) - Python is used for scripting for interacting with databases. Many modern SCADA start to support variations of python (Jython is used in Ignition).
In general is no end to the uses that Python has as an engineer particularly manipulating and cleaning large datasets. - Java, HTML, JavaScript, VBA are used extensively for developing highly customised operator interfaces (HMI). HTML and JavaScript is used by many of the modern SCADA system that use web based operator clients. Many older and legacy SCADA systems use VBA for HMI development such as inTouch, iFix, and Factory Talk.
Scripting and Shell Commands
- Linux Shell, Windows PowerShell, Windows CMD are heavily used during SCADA integration for setting up scheduled processes and automating tasks between servers. They are also frequently used as first-line tools for troubleshooting network adapters and communications issues.
Operating Systems
- Windows, Most SCADA and DCS runs on Windows server environments. Therefore it’s essential to know how to configure and manage users and group policies in the Windows Active Directory environment.
- Linux Distros, Linux type operating systems are often used for the emerging edge computing technologies. Also some modern SCADA products can be installed directly on Linux (e.g. Ignition). There is also an emerging practice reported by engineers in the community where virtual SCADA servers and clients are hosted on Linux machines i.e. Windows VMs hosted on Linux server.
Database and Historians
- Database management in the field of SCADA Database of some sort, is always used for process historian, alarm and events, and users; design, configure, and manage relational databases commonly used in ICS, such as SQL Server, Oracle, MySQL, and OSIsoft.
- Data Aggregation and Historian, involves gathering operational data of various types from multiple sources and storing it in databases. End users often prefer popular products like OSIsoft PI and AspenTech for aggregating and historising operational data from field devices and automation systems.
Industrial Networks
- SCADA Network Design, involves designing complex multi-topological industrial networks based on the spatial arrangement of ICS equipment, specifying cables, switches, and other network components. Develop comprehensive cable schedules and IP address plans, and implement appropriate segmentation using subnetting and VLANs.
- SCADA Network Troubleshooting, Troubleshooting, and commissioning various Layer 2 (L2) and Layer 3 (L3) network devices, such as servers, workstations, switches, firewalls, and routers.
- Application and physical layer communication protocols, such as OPC, Modbus TCP, DNP3, Ethernet/IP commonly used for SCADA integration.
- Network Diagnostic Tools, Modscan and other similar tools used for simulating Modbus slaves/masters, very commonly deployed for diagnosing and troubleshooting serial connections. Wireshark is used for deep level analysis of frames and packets, can be helpful for diagnosing system network performance issues and find the source of network issues by inspecting individual TCP/UDP packets.
- OPC Servers, functions as middleware enabling communication between industrial devices and software applications using the OPC standard. OPC servers are heavily used in SCADA integrations for consolidating data streams from diverse ranges of automation devices, providing a OPC interface to SCADA. Some commonly used OPC server products are KEPServerEX, Matrikon, Softing OPC Suite, Prosys OPC UA SDK and Cogent DataHub.
- OPC Tunnelling, OPC tunnelling is used extensively during SCADA integration especially in scenarios where OPC communication needs to traverse different network segments or pass through firewalls.
- Industrial Network Cybersecurity, involves designing firewalls and demilitarised zones (DMZs) that adhere to ICS cybersecurity best practices outlined in ISA 99/IEC 62443 standards. Managing SCADA network cyber security activities, including penetration testing, hardening, access control, vulnerability management, penetration testing, and patch management.
IT/OT Integration
- MES, developing SCADA interfaces for Manufacturing Execution Systems (MES) such SAP ME, Simatic IT MES, FlexNet and AVEVA MES.
- ERP, developing SCADA interfaces for Enterprise Resource Planning (ERP) such as SAP ERP or Oracle ERP.
- PLM, developing SCADA interfaces for Product Lifecycle Management such as Siemens Teamcenter or Dassault Systèmes ENOVIA.
- AMS, developing SCADA interfaces for Assent Management Systems (AMS) such as IBM Maximo or Infor EAM.
- SCM, developing SCADA interfaces for Supply Chain Management such as SAP SCM or Oracle SCM.
- Edge Devices, selecting and deploying edge computing devices such as industrial PCs, gateways, or edge servers at various locations within the industrial environment. Examples include UNO series, Dell Edge Gateway, Siemens Industrial Edge, Azure IoT Edge.
SCADA Platforms
This involves having hands-on experience and/or training with the common SCADA platform. The following is an example of some common skills required
- Being able to configure interfaces to various automation devices and systems.
- Setting up the SCADA database and historians.
- Configuring workstations clients and managing user access.
- Developing intuitive HMI inline with P&IDs.
Some examples of commonly used SCADA platforms are;
- WinCC (Siemens)
- VTScada (Trihedral Engineering)
- Ignition (Inductive Automation)
- iFIX (GE Digital)
- Intouch (AVEVA)
PLC Technologies
While it may not be mandatory to be a PLC specialist it nonetheless helps to have good familiarity with these platforms if you are work in SCADA and need to develop interfaces for exchanging data.
In most cases there will be some configuration needed within a PLC to support the data handoff to SCADA.
Engineers working in a more general control system role would need to be fully conversant in standard PLC programming languages (IEC 61131-3), particularly Ladder Diagram (LD), Function Block Diagram (FBD) and Sequential Function Chart (SFC).
Examples of common PLC are
- ControlLogix (Allen-Bradley)
- Modicon (Schneider Electric)
- TwinCAT (Beckhoff)
- MELSEC (Mitsubishi)
- RTU Platforms;
- SIMATIC RTUs (Siemens)
- SCADAPack RTUs (Schneider Electric)
- RTU2020 (Honeywell)
- STARDOM RTUs (Yokogawa )
Mental Attributes and Behaviours For a Career in SCADA
- Decision making – Finding a balance between thoroughness and timeliness in decision making, try to avoid rashness and excessive procrastination.
- Dealing with uncertainty – In such a complex domain as SCADA we may not always have perfect information. Try to understand the relationship between the impact of the unknown information on the outcome and the significance of the decision to be made.
- Imagining the worst case – For each design decision you make, try to determine the worst case outcome and apply comprehensive risk mitigation. Apply risk management concepts systematically and align all your decisions with safety and operational integrity.
- Interpreting Standards and Project Specifications – Interpreting standards, normative references and contractual project requirements. Having the ability to recognise and manage non-compliance issues. Using sound judgment and reasoning where standards are inadequate.
- Recognizing Limitations and Learning from Failure – Be aware of your personal limitations and know when you have wandered outside of your domain of expertise. Always record and learn from mistakes.
- Ethical Decision Making – Make ethical choices prioritizing safety and environmental concerns in SCADA operations. Not cutting corners!
- Systems Thinking and Interconnectivity – Understand operational, business, legal, and cultural contexts and how your role as a SCADA engineer either provides inputs or takes outputs from others. Understanding and managing the impact your decisions have across other disciplines. Try to have a holistic view, considering the entire system rather than focusing on individual parts, to understand how the system functions as a whole.
- Building Relationships – It’s essential to be able to build good relationships with your clients, stakeholders, and operations personnel. However, this must also be balanced with ensuring that you act in a way that protects your company’s commercial best interests and not to be coerced into doing ‘favours’.
What Industry Sectors Do SCADA Engineers Work In?
One of the fantastic benefits of pursuing a career in SCADA and industrial automation is the opportunity to work across diverse industries. I know several engineers who have spent time in their careers both on offshore oil production platforms and in high-tech biopharma facilities.
While much of the automation technology used across different industries is the same, the types of processes, regulatory standards, and workplace cultures can be very different. This diversity can make for a very interesting career, allowing you to find new challenges by moving between extremely varied industrial environments.
If you are agile and able to learn quickly, it is possible to transition between industry sectors. This adaptability contributes to making SCADA (and industrial automation) an extremely reliable and safe career. As one industry declines and workers are laid off, you can move into another industry that is growing.
A good example of this is seen with many automation engineers who worked in oil and gas during drops in oil prices and the decline of the local oil industry (such as the UK North Sea). Many of these engineers found immediate employment in the pharmaceutical industry, which surged due to COVID-19.
An example of some SCADA system applications within different industries include;
- Power Generation and Utilities – Grid management, substation monitoring
- Oil and Gas – Monitoring of pipeline networks, refinery processes, production platforms and storage facilities. Control of pipeline valves at remote locations.
- Water and Wastewater Management – Monitoring water treatment processes, distribution networks, and wastewater treatment plants, controlling weirs and valves to maintain levels.
- Manufacturing – Control and optimization of manufacturing processes, production lines, material handling systems, and quality control.
- Transportation and Infrastructure – Monitoring traffic control systems, railway signalling and airport operations. Data generated from SCADA is used extensible in this industry to plan for maintenance activities (predictive maintenance).
- Building Automation and HVAC – Control and monitoring of heating, ventilation, air conditioning (HVAC), lighting systems, and energy management in commercial buildings.
- Telecommunications – Monitoring the status of critical telecommunications infrastructures such as cellular towers, fibre optics, and network operations centres (NOCs).
- Environmental Monitoring and Agriculture – Monitoring of environmental parameters (air quality, weather conditions), irrigation systems, greenhouse operations, and precision agriculture.
- Food and Beverage – Control and monitoring of food processing operations, packaging lines and storage facilities. Interfacing with end-user ERP, MES and quality control systems.
What Types of Companies Do SCADA Engineers Work For?
The supply chain of SCADA systems involves many different companies, each with its own commercial obligations and functions, such as engineering contractors, vendors, and OEMs.
Fundamentally, all companies will be taking some kind of input, such as requirements, and providing an output, either in the form of engineering design or automation equipment, with the end user being the facility operations team.
Depending on the type of company you work for, your role will differ. Generally speaking, working with integrators and vendors will have you focusing on more specialized technical aspects, while working with large engineering firms and end-users will lead to roles that involve more oversight and compliance.
- Control System Integrators (CSI) – SCADA engineers with integrator firms take basic design inputs and requirements from clients, such as engineering contractors and end-users, and design, build, and deliver automation systems. This work can involve large lump-sum projects, application work, or ongoing operations support.
- Large Engineers Contractors (EPCs) – SCADA engineers working for EPCs develop basic SCADA designs based on process inputs and facility design. They manage the tendering process for vendors and oversee the contracts for control system integrators. Additionally, they oversee the development, witness testing, and inspect the delivered automation system. They also coordinate punch closure and handover to the end-user.
- End-User – SCADA engineers working for end-users are involved with defining project specifications, the basis of design, and regional regulations. They oversee and witness the evolution of SCADA design from concept to delivery, witness and approve design deliverables from EPCs and CSIs, and coordinate handover to the operations team.
Is SCADA Engineering a Highly Paid Profession?
Within the context of other engineering disciplines SCADA is normally a highly paid profession with average salary being at least 20- 50% more than average engineering salary in the USA. Traditionally there has always been a discrepancy between the demand for qualified automation engineers and the supply of qualified candidates.
What Factors Influence the Salary of SCADA Engineers?
- Industry: The industry you work in and the specific process for which you are delivering SCADA systems is a big driving factor. Processes that are highly complex, mission-critical, and where errors can cause significant business loss tend to offer higher salaries for the engineers working on them.
In these cases, SCADA engineers carry high levels of responsibility, as their decisions can have a major impact on end-user commercial interests and local facility safety. Examples include oil and Gas, Biopharmaceutical, and Nuclear Industries. - Region and Local Availability of Candidates: Some regions tend to have better or worse supply of SCADA engineers. This is due to the availability of education systems and university courses that produce graduates.
Also in some regions the local culture may be a big preference to enter different professions. Regions where there is a low supply of candidates or and low supply of candidates willing to relocate will drive the salary up.
- SCADA engineering has a Long Learning Curve: Graduates and interns are often allowed little access to live control systems due to the risk of commercial loss to the end-user caused by accidental plant stoppage.
Unfortunately, working in a profession that deals predominantly with high-value, mission-critical systems imposes limitations on the rate of competency development. This factor also limits the number of qualified candidates available or with enough experience behind them to do the required job without supervision.
- SCADA is a bit of a “Niche”: As a relatively young profession, Industrial Automation has struggled to establish its own identity among the classical engineering professions such as Electrical, Process, and Mechanical engineering.
In most Western economies, university subjects and majors linked to Industrial Automation, such as applied physics, mechatronics, and control theory, have experienced a decline in popularity as students are increasingly attracted to emerging fields like Data Science and AI, which tend to have greater appeal.
These factors make SCADA a bit of a niche profession that is both difficult to get into and not widely known. Consequently, this factor introduces a limit on the number of candidates who will enter the profession simply because they are not even aware of it.
What Education and Training Do I Need for a Career in SCADA
SCADA engineering and the profession of Industrial Automation have a complex and diverse range of skill sets, drawing from academic disciplines like applied physics and control theory while also requiring non-academic technical skills like PLC programming, which are more associated with trade school.
There are generally speaking very few dedicated university degrees available for the automation and control. In university you can learn the underlying fundamentals in courses such as Mechatronics, Applied Physics, Instrumentation, Computer Science. However most universities don’t have PLC, and automation equipment, as this is considered outside of the domain of academia.
Practical training for PLCs and SCADA is acquired either in trade schools or “on the job”. As a fresh graduate, you will hopefully have the opportunity to “play” with PLCs in a controlled environment. Most automation companies have a staging area with test rigs and simulators that can be used for training purposes.
In addition, there are many online courses available that cater to a range of different budgets.
See our list of the best value PLC training courses here
Automation suppliers and integrators invest heavily in internal training and have highly systemized workflows for training their workforce. This is necessary because their technology stack is often extremely complex, and in many cases, such as DCS, it is also highly proprietary.
The good news is that most of the technical skills listed in the previous chapter can be learned from freely available content and training courses online. It is up to the individual to take the time to learn and continue learning both to enhance their skills and to keep up with new technologies as they emerge.
What are the Benefits of a Career in SCADA?
Travel and Adventure
Working on SCADA systems often involves site work and a fair bit of travel, as well as staying in hotels in highly industrialized regions or sometimes remote areas, such as offshore platforms.
For young engineers who haven’t seen much of the world, this can be a great part of the job as you get paid to travel. Depending on your role, you may be deployed locally or even internationally; server engineers for large automation suppliers can be deployed anywhere on the globe.
Most people would agree this is better than being stuck in a cubicle farm and taking the subway to work.
However, there are two sides to this. For more senior professionals, this often becomes tiresome, especially with the constraints of family life and trying to keep your home life from descending into chaos while you’re away.
Unfortunately, for many people who work continuously in field service and commissioning roles, this has some adverse outcomes for marriage, alcohol abuse, and damaged relationships with family and friends.
It’s highly individual how you approach this, but it’s something to consider depending on your current age and where you are in life.
Job Security
Something that is universally agreed upon is that if you are a qualified and experienced engineer with skills in SCADA integration, you will have a job for life. Why? Because there will always be a need for industrial automation, and the global automation industry is, in fact, surging.
In addition to the factors previously mentioned, such as the low supply of candidates and the low interest in people taking up the profession, this means you will generally always have some options available.
There is also little chance that any of the SCADA integration roles will be absorbed by AI anytime soon. Even if AI is used for programming, there is still too much hands-on work needed in the field of SCADA. Most end-users who have any concern for their cybersecurity posture are repulsed by the notion of allowing AI to run rampant on their facilities.
Good Salary
SCADA engineers and automation engineers in Western economies are generally very well-paid professions, with the average salary being at least 20- 50% more than the average engineering salary in the USA. Traditionally there has always been a discrepancy between the demand for qualified automation engineers and the supply of qualified candidates.
What are the Downsides to a Career in SCADA?
Too much Travel and Site Work
Not everyone likes to spend time on-site or travel away from home. For more senior engineers with families, this can be challenging and lead to personal issues.
There is also a lot of fatigue associated with travelling constantly and staying in hotels.
Large companies normally have dedicated service departments that undertake these kinds of roles while engineers remain at headquarters and provide remote support. However, this may not be the case in smaller automation companies, where engineers might be required to handle both on-site and remote tasks.
Unpleasant Site Conditions
The conditions in industrial facilities are not always very nice. For example, if you are working in remote locations, you may have to share accommodation (bed and board) with other workers. If you are working overseas, there may be a significant cultural adjustment that is hard to sustain mentally for long periods.
Site conditions are not always pleasant. Automation technology is used by all industries, not just in clean, modern pharmaceutical plants and car plants.
You may find yourself in some fairly nasty environments exposed to strong smells, noise, and extreme environmental conditions.
- Rendering Plants – Process animal byproducts into usable materials like tallow, grease, and meat and bone meal. The process of breaking down animal parts can produce extremely strong and unpleasant odours which often induces spontaneous vomiting.
- Pulp and Paper Mills – The process of turning wood into paper involves the use of chemicals that can emit strong, sulfurous odors (“rotten eggs”).
- Wastewater Treatment Plant – Processing sewage and industrial wastewater, which can emit strong smells from decomposing organic matter.
Boredom on Long Projects
Large SCADA integrations can take a long time to design, build, and commission, while large capital projects can take years.
This can lead to engineers becoming bored, disillusioned, and disengaged. Additionally, as is the case with most engineering professions, you may spend a lot of time on paperwork, dealing with compliance issues, materials, HR matters, and general admin.
Unfortunately, this is the reality for most engineering professions, especially if you work with major engineering contractors on large projects (EPC). In such cases, you will likely be in endless meetings, dealing with reporting, and playing email tennis with vendors and subcontractors.
Stress and Overload
Working with mission-critical systems can be extremely stressful. Some examples of why;
- You may have to undertake risky SCADA modification on live system changes that can cause plant stoppage.
- You may get put under a lot of pressure by being mobilised to a facility to fix a SCADA issue that prevents plant production and costs the end-user millions in losses daily.
- You may face tight deadlines that coincide with other critical milestones.
- You may have limited support available, and fatigue from travel and poor sleep can compound these issues.
- You may have to deal with toxic working environments, such as end-users refusing to take ownership, non-conformity issues, vendors unwilling to provide support, and end-users requesting modifications outside the agreed scope
Conclusion
A career in SCADA and industrial automation can be incredibly rewarding, providing a diverse array of opportunities across various industries and the chance to travel globally, working within some incredible industrial facilities.
If you have a solid technical background in IT and computer science, finding your footing in SCADA will not be difficult. However, working on SCADA, like any mission-critical system, carries a degree of stress and significant responsibility.
If you thrive in high-responsibility roles and enjoy taking a measured, careful approach to your work, SCADA is an excellent career choice.
Despite the long learning curve, technical demands, and occasionally tough working conditions, SCADA engineering offers job security, high remuneration, and a dynamic work environment.
If you are someone with a strong adaptability, eager to learn, and ready to face new challenges, a career in SCADA can be highly fulfilling. With the right skills and mindset, you can navigate the complexities of this field and build a successful, long-term career in industrial automation.
Share
Facebook
X
LinkedIn
Telegram
Tumblr
Whatsapp
VK
Bluesky
Threads
Mail